Skąd w Warszawie firma zajmująca się zaawansowaną elektroniką, która dostarcza produkty na kilka kontynentów? Historia zaczyna się w 1995 roku. Wtedy jeden z profesorów Politechniki Warszawskiej - wraz z trzema doktorantami - założył firmę Advanced Power Systems (APS).
- Firma rozpoczęła działalność z założeniem zaprojektowania i wyprodukowania nowej rodziny systemów zasilających jej procesy, dla holenderskiej firmy działającej na rynku high tech. Polskie konstrukcje przyjęły się tak dobrze, że posypały się kolejne zamówienia i firma zaczęła się szybko rozwijać. W 2007 roku część firmy APS została połączona z niemiecką firmą TRUMPF Huettinger. Owocem tej biznesowej decyzji były nowe inwestycje, na przykład kolejne budynki: w Zielonce, w Markach i teraz na Targówku – mówi nam dr Paweł Ozimek, prezes TRUMPF Huettinger w Polsce, który był jednym z pierwszych pracowników firmy.
„Wysyłamy na cały świat”
Spotykamy się w nowej fabryce na warszawskim Targówku. W potężnym budynku, podzielonym na strefy, pracuje ok. 600 osób. Na dwie zmiany. Powstaje tu siedem grup produktów – zasilaczy, które wcześniej są wymyślane i projektowane w centrum badawczym w Zielonce. Co ciekawe, fabryka jest tu od około roku. Wcześniej zasilacze też powstawały w Zielonce, ale produkcja była tak duża, że trzeba było znaleźć nowe miejsce. Cały zakład przeniesiono… w weekend.
Warszawska Dolina Krzemowa. Ich produktów używają giganci el...
Zaglądamy do środka. Na miejscu produkcja wygląda w następujący sposób. Najpierw niewielkie podzespoły łączy robot „Deprag”. Zajmuje się zasilaczami chłodzonymi wodą. Przy jednym urządzeniu „pracuje” 80 minut. Ten robot ma już dziesięć lat, jego następca – pracujący już równolegle – robi to samo w… 9 minut.
Następnie przyszłe urządzenia montowane są przez pracowników, którzy z odpowiednich modułów budują zasilacze. Potem przechodzą one testy. Najpierw low voltage, a po założeniu obudowy także sprawnościowe i wysokonapięciowe. W międzyczasie każde urządzenie jest sprawdzane przez kolejnego robota, który szuka błędów. Jak słyszymy, jest w tym perfekcyjny, ponieważ sztuczna inteligencja na bieżąco się uczy.
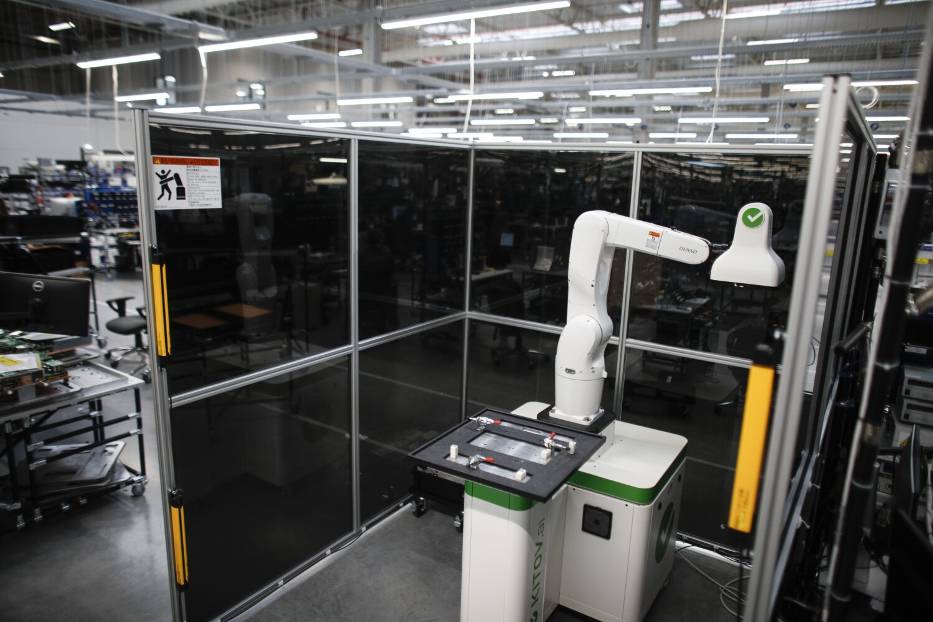
- W tym budynku pracuje kilkanaście linii produkcyjnych, z których największe produkują pięćset zasilaczy tygodniowo wysyłanych na cały świat. Nie mówimy tu o małych zasilaczach do ładowania telefonów komórkowych, ale o dużych systemach, o mocach od kilkunastu do kilkudziesięciu kilowatów, o wadze przekraczającej czasem dwieście kilogramów. Są one wykorzystywane m.in. do produkcji paneli fotowoltaicznych. Kupując dziś panel fotowoltaiczny w sklepie, mamy ponad 90 proc. szans, że został wyprodukowany przy użyciu naszej technologii. Od 2018 roku wyprodukowaliśmy i wyeksportowaliśmy ponad 100 000 sztuk takich zasilaczy – tłumaczy nam dr Paweł Ozimek.
Systemy zasilające, które powstają w Warszawie, wykorzystywane są w przemyśle zorientowanym na technologię plazmową. Jak słyszymy, chodzi o to, żeby wykorzystać plazmę do rozbicia materiału na cząstki elementarne i osadzić go na cienkiej warstwie, mierzonej w nanometrach. Wykorzystywane jest to niezwykle szeroko przy np. :
- produkcji półprzewodników i układów scalonych
- ekranów LED i OLED, wyświetlaczy telefonów
- pokryć dekoracyjnych (np. telefonów)
- utwardzenia powierzchni metalowych (np. wiertła czy łopatki turbin silników lotniczych)
- produkcji panelu fotowoltaicznych.
- Jak mówi jeden z naszych najbardziej doświadczonych pracowników, nie problem jest zrobić zasilacz, tylko fabrykę zasilaczy. Dochowanie i powtórzenie standardów dla każdego wyprodukowanego urządzenia jest wyzwaniem. A my do tego celujemy w rynki najbardziej wymagające. Na tle konkurencji wyróżniamy się nie tylko nowatorskimi technologiami w naszych produktach, ale również wysokim stopniem automatyzacji produkcji – tłumaczy dr Ozimek.
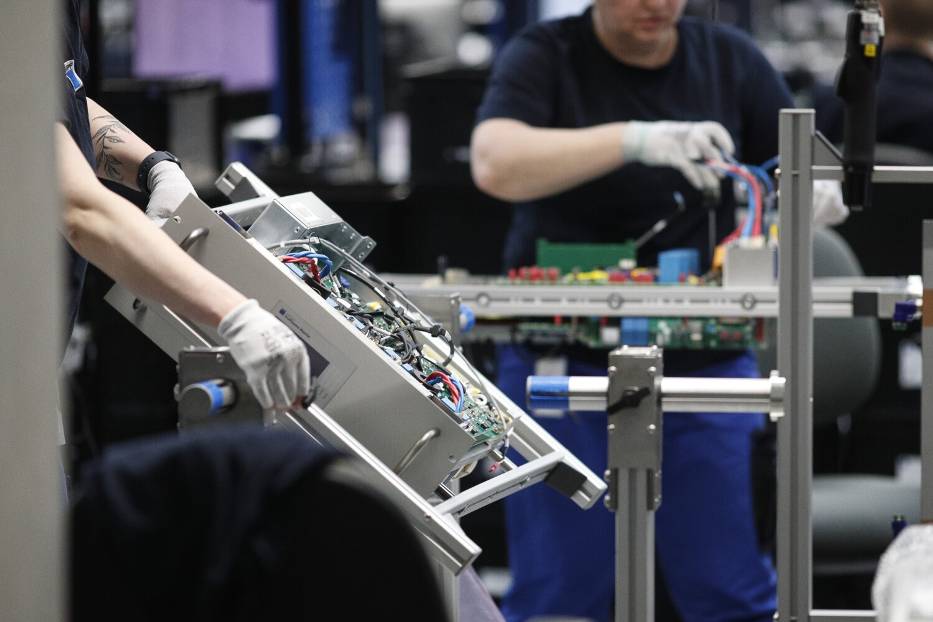
„Mamy 14 doktorów i 5 otwartych przewodów doktorskich”
Rozwój firmy jest tak gwałtowny, że pewnym problemem stała się rekrutacja pracowników. W ciągu półtora roku podwojono zatrudnienie. Teraz, w perspektywie kolejnego roku, znów pracowników ma być dwa razy więcej. Już wiadomo, że na Białołęce otwarta zostanie nowa hala, gdzie produkowane będą generatory na rynek fotowoltaiki i laserów. Ale szefostwo już myśli o kolejnej lokalizacji.
- Obecnie w trzech lokalizacjach (Zielonka, Marki i Warszawa-Targówek – red.) zatrudniamy około 1400 osób w tym ok. 400 inżynierów. W tej chwili mamy też czternastu doktorów i pięć otwartych przewodów doktorskich. Prowadzimy tzw. doktoraty wdrożeniowe, co oznacza, że osoba robi doktorat pracując w naszej firmie nad konkretnym projektem. Kilka miesięcy temu, na podstawie pracy w naszych laboratoriach, jeden z pracowników zamykał rozprawę doktorską. W sumie z wyższym wykształceniem mamy aż 54 proc. załogi. To znacznie wyższy poziom niż średnia w przemyśle. Wynika to przede wszystkim z wysokiego stopnia zaawansowania technologicznego naszych produktów wymagających specjalistycznej wiedzy przy ich projektowaniu i produkcji - uruchomieniu, testowaniu i kalibracji – wyjaśnia dr Ozimek.
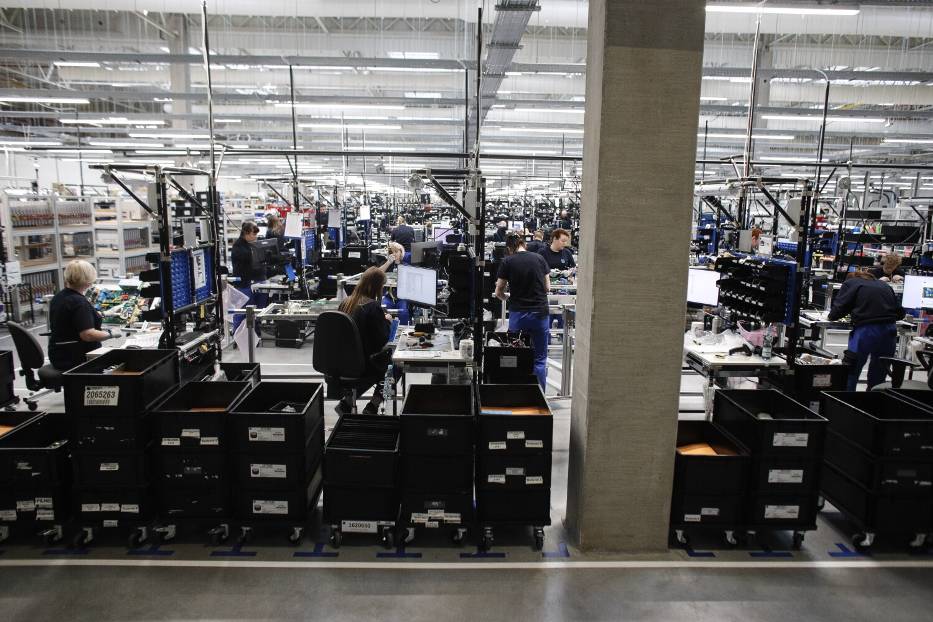
Firma współpracuje z Politechniką Warszawską, a wśród studentów szuka specjalistów do ośrodka badań i rozwoju. Tam powstają projekty nowych urządzeń, a także testowana jest technologia. Przykładowo, w niektórych stress testach temperatura urządzenia zmienia się o sto stopni (!) na minutę. W ten sposób szuka się słabego punktu, który się eliminuje.
Na Politechnice powstało już niewielkie pomieszczenie dla studentów, których zatrudnia TRUMPF Huettinger. Firma prowadzi też program mentorski oraz stypendialny. Prezes polskiego oddziału liczy, że ta współpraca z roku na rok będzie coraz lepsza. Chciałby, żeby jak najwięcej nowych rozwiązań, technologii przyszłości, powstawało w Polsce. Przykład systemów zasilających z 1995 roku, wymyślonych przez naukowców związanych z Politechniką Warszawą, pokazuje, że jest to możliwe.

META nie da ci zarobić bez pracy - nowe oszustwo
Dołącz do nas na Facebooku!
Publikujemy najciekawsze artykuły, wydarzenia i konkursy. Jesteśmy tam gdzie nasi czytelnicy!
Dołącz do nas na X!
Codziennie informujemy o ciekawostkach i aktualnych wydarzeniach.
Kontakt z redakcją
Byłeś świadkiem ważnego zdarzenia? Widziałeś coś interesującego? Zrobiłeś ciekawe zdjęcie lub wideo?